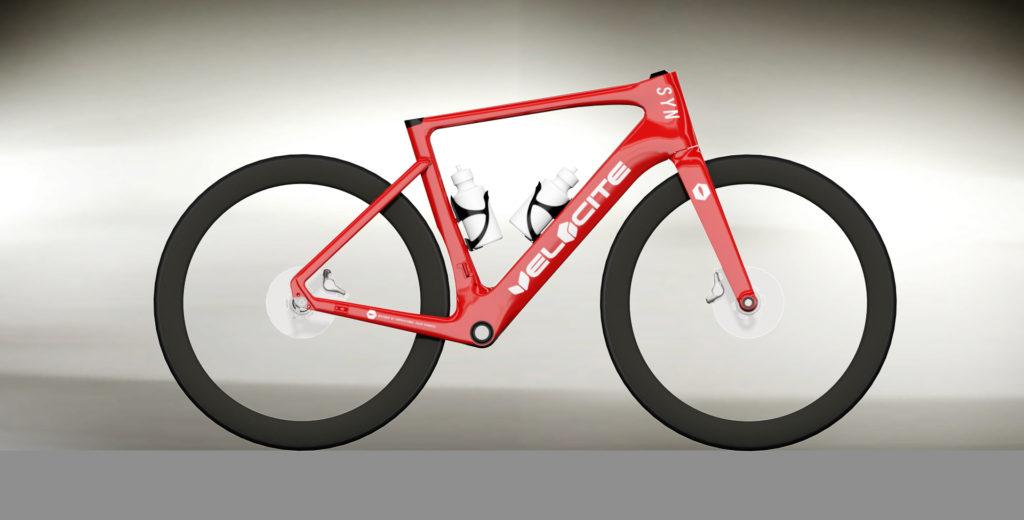
In a nutshell, there are three overarching principles that guide our product design and development:
1. Maximum Stiffness and Performance. Achieve the optimal stiffness for each product, even if it means increasing weight, by using well understood laws of physics, material science, and mechanical design. Only make one version of the same product – what our sponsored riders are riding is the same product that you can buy.
2. High Rider Weight Limits. Nominally, anyone of up to 110kg weight should not have any issues with the use of our equipment, but will experience accelerated wear and tear with wheels due to basic physics that govern their mechanical performance.
3. Live Testing Program. In addition to extensive machine testing, always conduct live product testing before releasing a new product to the market, even if it means causing delays and design changes. After product release, proactively seek feedback from the customers and sponsored riders and seek opportunities for continuous improvement – even within the current product life cycle.
These principles guide Velocite on its path to deliver the best possible bicycle products. We mean it when we claim “Ride Velocite, Feel Invincible”.
Maximum Stiffness and Performance
The optimal amount of horizontal (side-to-side) and torsional frame flex is zero. Horizontal and torsional bending of the frame saps energy and negatively affects the bike handling.
A degree of vertical flex (compliance) is desirable. Due to the overall bicycle hysteresis (damping, or energy loss), vertical flex enhances the rider comfort when traveling over a rough surface.
It is important to realize several important characteristics of a bicycle frame and the laws of physics that determine its performance. Without going into the governing physics theorems too deeply (for those that are interested, refer to “Hooke’s Law“, “Harmonic Oscillator“, “Elastic Hysteresis” and “Damping“), consider that a bike’s comfort, as derived from its ability to absorb road irregularities, is caused by its ability to dissipate the forces – it loses energy. Thus, when the bike is subjected to torsional loads due to pedaling, a flexible frame similarly dissipates the forces as a result of pedaling – it wastes your energy. There are no exceptions and no valid counter theories.
Therefore, bike frames that have significant horizontal and torsional flex negatively impact your performance and riding enjoyment.
How do we maximize lateral and torsional stiffness?
First, we need to clarify that the most significant forces acting on the bicycle are not lateral or even vertical, they are almost invariably “out-of-plane” thus resulting in torsional loads on the frame. This is especially true for the two most significant parts of the frame: bottom bracket and the head tube. Both of these sections of the frame are exposed almost exclusively to torsional loads. It is incorrect to assume that because your feet move up and down that the frame is loaded in the same fashion. It must be considered that your feet are pressing on the pedals some distance away from the frame (exactly how far depends on the BB tread/Q-factor) causing a torsional load to the bottom bracket that is translated into horizontal flex, the extent of which depends on the frame’s torsinal stiffness.
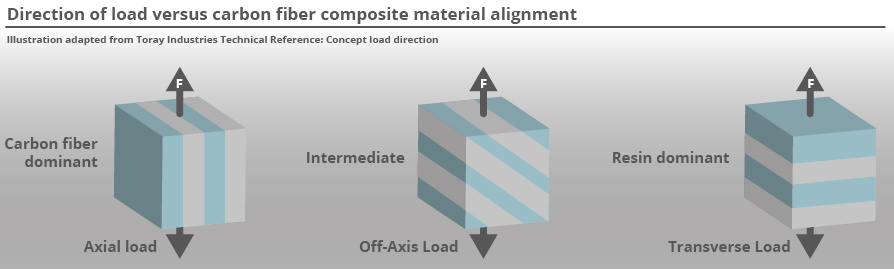
With the bicycle frame, especially those made from carbon fiber composites we have two main methods for ensuring maximum torsional stiffness:
- Optimal Tube Shapes and Structural Design
- Optimal Carbon Fiber Layup and Manufacturing Process. Read more: Carbon FiberTube Shapes and Structural Design
Velocite understand that the bicycle frame works as a unit, thus every part of the frame must be of sufficient strength and torsional stiffness. When riding a bike you experience the benefits of this approach through increased confidence and better control.
The defining elements of our design philosophy are:
1. 1.5″ oversize tapered head tube
2. Full length bottom bracket shell
3. Stiff rear triangle
Oversize head tube provides direct benefit to the structure of the frame by increasing the available surface area for the down tube section. In monocoque design this is particularly advantageous since it allows extra carbon fiber to be laid down in optimal directions. One other often overlooked benefit of a 1.5″ head tube is that it allows the fork crown to be made larger and at a small increase in weight, stiffer than an equivalent 1 1/8″ fork
Full length carbon or alloy BB30 shell is often lighter and always stiffer than separate alloy cups. In fact it is effectively rigid providing perfect support for the crank axle.
While utilizing very thin seat stays in the rear triangle is a popular design choice, we believe that this is not the best way to deliver optimal performance. Thin seat stays are less strong both vertically and horizontally and it is not possible to make their strength directional due to the negligible profiles. This lack of strength is desirable with respect to increasing vertical compliance and decreasing road vibrations, it is however very undesirable when it comes to delivering true high performance torsional stiffness, and even optimal rear wheel tracking. Velocite frames therefore utilize the strongest available designs for the rear triangle given the target end use of the frame.
The geometrically strongest shape for resisting torsion is a cylinder. The ability of hollow shapes to handle torque forces depends on the distance of the surface of the shape from the geometric center of the shape. The illustration shows that when comparing a circular shape versus a square shape, more of a circle is further from the center of the shape. This means that for given weight of the tube, a cylindrical tube will be stronger under torsion, all other things being equal.
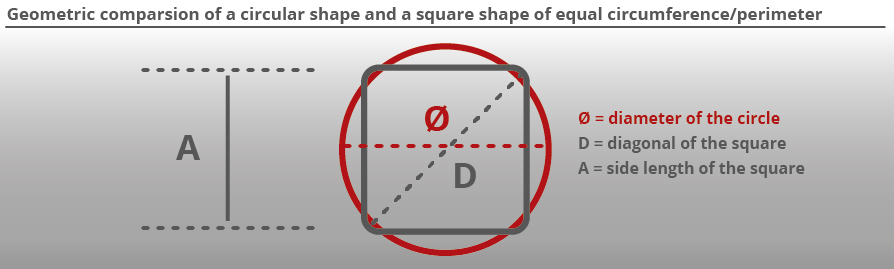
Therefore, when space allows, you will only ever see cylindrical shapes in down tubes of Velocite bikes. While square, polyhedral, or multi-shaped down tubes are fashionable, they are structurally inferior to cylindrical, or continuous surfaces. Such square, or polygonal tubes are a lot more effective in handling perpendicular loads, or as far as a bike is concerned, vertical and horizontal movement. This is counter productive when it comes to comfort which is in part delivered through vertical compliance of the frame.
Using square, or polygonal shapes in carbon fiber composite parts is also not optimal since the main strain under torsion is shear strain, and in such shapes the shear strain is concentrated in the corners (Read more: Deformation) Carbon fiber, due to it having strength only along the fibers is not particularly well suited for managing shear strain because it can act transverse to the fiber length. Thus in case of shear, regardless of the underlying carbon fiber layup, some of the strain is actually borne by the resin part of the composite, not the carbon fibers. In essence, this means that when using square or polygonal shapes, the main advantage of carbon fiber which is its exceptional strength in tension is not fully utilized.
Read more about geometric shapes and torque here: Lous L. Bucciarelli, Engineering Mechanics for Structures: Chapter 6 Stresses/Deflections Shafts in Torsion
What about making the bottom bracket larger to increase stiffness?
In modern frames, the bottom bracket does not flex. The maximum amount of flex is observed at the bottom bracket, but this is not because the bottom bracket itself is flexible, it is due to the rest of the frame allowing the bottom bracket to move side to side (actually, rotate around a virtual point some 5-20cm above the bottom bracket depending on the frame’s stiffness) under torsional loads. Therefore making the bottom bracket larger, wider, or taller will not result in increased frame stiffness, unless other frame elements are likewise strengthened.
Increasing the surface area by making the bottom bracket larger serves to spread the shear strain. However, because carbon fiber composite is an anisotropic man-made material, its properties can be changed at will just by changing the layup. Thus, adding carbon fiber layers achieves the same improvement in shear stress management without increasing aerodynamic drag, or causing incompatibility with existing bicycle components.
Read more about torsion and shear in this educational article from The University of Cambridge: Bending and Torsion of Beams
What about frame comfort, stiff frames are uncomfortable?
Rider discomfort that can be contributed to the bicycle frame, if the geometry suits the rider and the riding position is correct, is a result of two factors: high frequency vibrations coming from the road surface, and the failure of the frame to absorb larger bumps due to limited vertical compliance. Torsional compliance does not determine the amount of comfort, but the excess torsional flex will contribute to discomfort due to poor handling.
1. Vibration damping: Velocite carbon fiber layup is very complex and uses from 5-13 layers of carbon fiber of various stiffness moduli (Young’s modulus). Besides achieving the class leading stiffness, this type of layup also successfully damps the high frequency vibrations. Carbon fiber composites have inherent good vibration damping properties due to their low specific density and the damping ability of the resin part of the composite. One other factor that helps manage the undesirable vibrations is the continually variable thickness of the side walls in Velocite frames due to the variable layup. This means that different parts of the frame have different mass and therefore different resonant frequencies, further damping the vibrations.
2. Vertical compliance: Cylindrical, continuous surface shapes allow greater amount of vertical compliance than the square shapes, thus even though Velocite frames are torsionally stiffer than frames that use square, or polygonal shapes, due to the use of cylindrical continuous surface profiles they have a degree of vertical compliance that can result in better rider comfort.
High Rider Weigh Limits (nominally 110kg)
In structural design of bicycle parts it is important to consider the loads that the part will be subjected to in order to ensure that the part will not fail during normal use. The higher the rider’s weight (mass actually), the higher the load that the part has to withstand (Newton’s Second Law of Physics). The loads are also dynamic, meaning that they change as the part is being used. During rapid acceleration, or deceleration the load on the part changes. By careful analysis and dynamic testing it is possible to design parts that are exceptionally light and yet strong. The temptation then exists to make the parts even lighter by stipulating rider weight limits. Parts designed to withstand less loading can be made by using less material and by using more high modulus carbon fiber (NOTE: refer to tensile strength versus tensile modulus: Carbon fiber). While both of these approaches are valid, they can result in parts that fail unexpectedly.
Velocite deisgns the parts to withstand very high resting and dynamic loads. Even with our lightest products such as the Geos frame, or the TLCS31 seat post there are no rider weight limits when the parts are used for intended purpose. We conduct our machine testing at high loads, and subject all parts to extensive live testing with some test riders weighing in excess of 100kg.
Live Testing Program
Even though all this focus on science, engineering and numbers may appear somewhat removed from the joy of riding a great bike, Velocite is all about making the rider feel invincible. We believe that we can deliver greater enjoyment to the rider by following well established principles.
To make sure that what we are observing on the testing machines and in software actually works in reality, every one of our key products goes through a long term live testing stage, sometimes lasting for up to 9 months. Our test riders represent a wide cross-section of our customers, from elite level pro riders, to recreational riders, across all age groups, continents and nationalities.
They are tasked with evaluating key performance aspects of each product when used in normal riding and race conditions. Everything from ease of assembly, fit and finish, durability, and even crash worthiness is assessed. Their feedback is used to either confirm our product specifications and move to mass production, or to make structural and even design changes in order to achieve the target performance level.
This indeed means that not all test feedback is positive, and that some products may get delayed as a result while we are making required changes. We believe that this is a good thing so we refuse to rush something to the market that does not exceed the performance of its peers, or at least provides comparable performance at a much better value.
An example of design changes that were made as a direct result of extensive live testing is the Velocite Geos lightweight road frame. Below you can see the structural changes between the live testing prototype on the left and the final version on the right. The final Velocite Geos frame gained a BB30 bottom bracket, much larger chain stays, and (invisible) extra carbon fiber layers near the head tube and behind the bottom bracket. Other changes were ergonomic with through the head tube cable routing and internal rear cable routing.
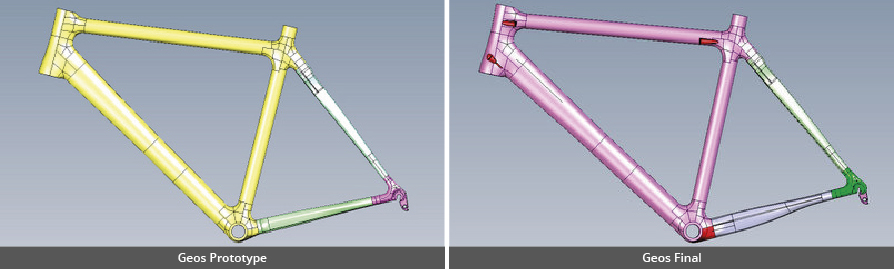